The Bleeding Edge of Simulator Technology
- GlobalSim
- Apr 22
- 7 min read
Updated: Jun 4
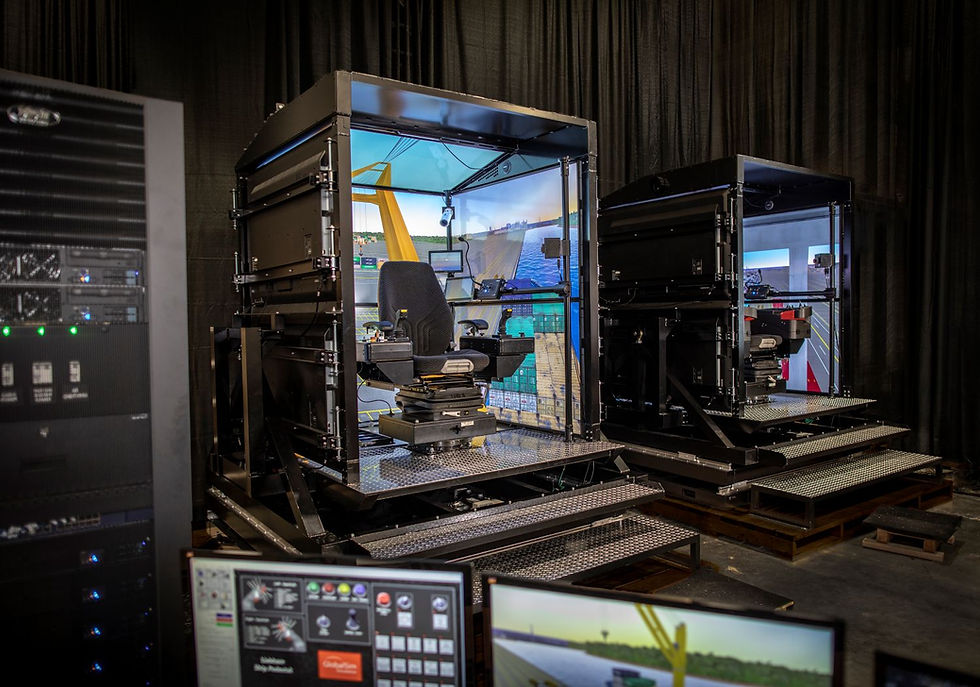
GlobalSim was founded in the early 1990s with a philosophy centered on technology. Over our entire history, we have remained committed to the idea that high-fidelity simulation is one of the greatest tools to increase safety and efficiency.
Simulation takes on many forms, varying more with every passing year as technology advances. From homebrew desktop programs to room-sized, full-mission cabins, simulators have one aim: to provide as immersive an experience as possible through the use of graphical fidelity, true-to-life programming, and tactile hardware. With the right setup, a company can train anyone on any vehicle without the same risks or costs of on-site operation.
What amplifies the reality of the experience, though? What technological advancements have impacted the industry most over the years?
In this article, we will cover a brief history of simulation technology, how GlobalSim is leveraging that tech to push what’s possible, and which key aspects of technology create the most immersive experience.
A Brief History of Simulation Technology
It is sometimes easy to forget we are always at the forefront of technology. Looking back, we can think certain technologies were downright quaint compared to what we have today, yet it was always the best we had at the time. The reality is that how a company chose to use the tools at hand in a given moment usually defined its success in later tech booms. Let’s take a look at how these tools have evolved over the past two decades:
2000s
The early 2000’s was the age of the in-house build. Technology grew more capable and available to companies everywhere, though without the constant cloud communication we enjoy today. There were also very few resources for pre-built engines or codebases. Industrial leaders hired developers to build whole engines, assets, and programs from scratch.
This homebrew mentality fueled a lot of innovation and creativity in the space. Companies took big swings in investment to experiment with new tools and make better simulators.
In 2005, GlobalSim delivered its very first crane simulator system utilizing plasma screen technology. While its sophisticated, physics-based system was cutting-edge, the graphical fidelity for true immersion was… archaic at best when viewed through today’s lens. We had to make sure no asset was made of more than 100 polygons—otherwise, the system would crash!

2010s
Where 2005 was the age of the in-house build, 2015 was when foundational engines like Unity and Unreal made building a simulation program easier than ever.
This made the market more competitive. Anyone could program their own simulator once they learned how to use a foundational engine. However, only a few could claim the kind of immersive fidelity required to build the best simulation rigs.
Between the two engines, GlobalSim chose Unity, primarily from a usability standpoint. Unreal’s graphics at the time were, well, unreal—but we prioritized a focus on realistic physics with a more approachable engine (which was a better fit for our global audience). Shortly after, in 2016, GlobalSim introduced the industry’s first virtual reality (VR) crane simulator, seen in this video from the time.
2020s
The COVID pandemic looms large in the history of everything. The echnology sector suffered from the same shipping issues as the rest of the world, but the constraints also resulted in an explosion of innovation across remote and cloud-based collaboration. In an isolated world, companies that pivoted to off-site work, consultation, and development made lemonade out of lemons.
With these advances, companies built and shipped systems to clients with instructions on set-up. Once set up, remote access allowed for active patching, troubleshooting, and implementation without in-person, on-site installations.
GlobalSim continued its work safely and efficiently—installing full mission systems around the world from Felixstowe, UK, to Tauranga, NZ.
Major Tools of Today’s Immersive Experiences
Now in 2025, we’re seeing three key areas where technology is having the biggest impact: VR immersion, graphical fidelity, and global networking through cloud computing. No matter what type of simulator a company invests in, it is important to examine each of these areas of technical ability to make the most confident choice.
VR
VR hit its stride over the last 10 years through accessible, handheld peripherals for nearly any consumer who owns a desktop. However, the goggles and hand controllers seen in advertisements or big box stores only represent one way VR can work. Virtual reality, with a more advanced setup, can also include surround sound, multiple screens, and physical hardware designed to rumble or shift alongside a digital program.
GlobalSim specializes in taking the technology at hand to create hyperreal immersion, and VR is no exception. It is not enough for a trainee to see highly detailed vehicle components on their screen behaving with real-world physics—we want trainees to feel the simulation and build useful muscle memory before the real thing. VR offers a valuable tool in this mission by making it possible to drive home the “fear factor.”
The reality is that once in the field trainees will be operating enormous equipment that costs millions of dollars around dozens of other workers. It is important for them to feel the machinery lean under heavy loads to get a sense of how high up they’ll be, to feel how the wind might compromise their position, and to realize exactly what missteps could cost. All of this isn’t possible with VR alone, but in combination with a motion base simulator or full-cabin simulator an immersive experience can be created that enables a trainee to not only learn how to operate a crane but to respect the gravity of the situation (no pun intended). With the right physics, programming, and peripherals, a simulator can pitch a trainee into a catastrophe that feels dangerous without the actual danger.
VR, at a smaller scale, can also be an affordable tool to power up basic training. Full-mission systems are expensive and take up a lot of space, but the commercially available VR systems that plug into a desktop allow a company to run multiple training sessions in parallel. No matter what level of simulation is at hand, in 2025, VR is somehow in the mix. In fact, in the last 5 years, nearly all of the systems we’ve installed have included a VR component.
Satellite Data / Accurate Models
Many clients prefer simulators programmed to match the actual job site, and technology has now advanced to make this level of customization an achievable reality. In the early days of GlobalSim’s operation, there were no remote satellite images nearly accurate enough to create high-fidelity working environments for our customers. Previously, if a high level of customization was required, we would need to send engineers out to each site to hand-measure dimensions and take pictures to allow us to provide a true-to-life experience within the simulator. With today’s high-resolution satellite photos, our simulations can accurately approximate job sites without the on-site visit.
Accurate models are likewise vital to the immersiveness of an experience. It is difficult to believe you’re training on the real deal when freight containers look like chunky, cartoony boxes. Similarly, if the main load line on a crane fails to sway as a trainee turns the operator cab, they are not training with reality in mind. At GlobalSim, we achieve this realism through the use of these advanced tools as well as the expertise of our diverse team, which includes a math PhD and physics specialist to ensure we’re creating hyperreal simulations.
With our highly experienced team and 2025’s photorealistic modeling tools, we are now able to render beautifully built assets that can be completely custom to the client. Some simulators go so far as including torn upholstery in seating or even discarded soda cans from the prior shift—just to more vividly bring the trainee into the scene. We program the sunlight so that a trainee can block it with their hand to see better! These visual advancements, whether on a desktop screen or a full-mission cabin, provide trainees with a better experience and more understanding with each session.
Cloud Technology
Cloud technology, with the inception of Amazon Web Services, was originally designed to allow computer engineers to share codebases between global locations. Today, we have a global network of servers that allow remote saving and retrieving at every level of computing.
In the simulator business, cloud technology allows providers to interface with their clients around the world. It provides an easy way to patch, download new simulations, and implement repairs without costly on-site visits. It is faster and less expensive for everyone involved.
Another major benefit of cloud computing in the simulator industry is that we (and our clients) are able to track metrics, record progress, and analyze data between their trainees to tailor learning experiences. Cloud computing has advanced enough that we recently released an entirely cloud-based simulator service for any company with the training computer to host it!
Where accurate models allow for visual clarity and virtual reality supports overall immersion, cloud technology is what allows anyone around the world to invest in training simulators and remain confident in them for years to come.
The Future Ahead
Technology has come a long way over the years, and it has revolutionized every aspect of simulators. What the future will bring is difficult to predict, especially with how quickly things change regarding technology, the industry, and the economy. We do know that computers will continue to get more powerful and innovations in physical simulation will continue to blur the line between the simulator cabin and the real deal out on the docks.
Since its beginning, GlobalSim has been on the bleeding edge of technology, pushing the industry and pioneering the very best in simulation. Today, our specialty revolves around customization in simulator development, and we intend to continue forging the brand new (and best) in training simulations for cranes and heavy machinery.
Commentaires